Hot
Air Dryers
Here are two versions available, "Economic" and "CE", both
are suitable for the continuous drying of 8 to 800kg/hr of general purpose
plastic granules. This series of dryers can be either machine mounted, or
floor mounted. Electrical circuit of the CE version is built to comply
with CE safety requirements, optional protective cover over the heating
chamber and double-skin hopper are normally fitted as standard. Insulated
hopper and higher heating capacities (dry up to 170¢J) can be fitted as optional
equipment to form "Hi-Heat" range with the CE version. Both versions
are able to fit with either microprocessor or solid-state control system.
|
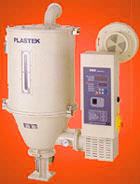 |
|
|
Dehumidifiers
Here are two versions available, "twin-tower" and "honeycle",
both are suitable for continuous drying of hygroscopic materials while incorporate
with a hot air dryer. The twin-tower version delivers dried air of
down to -40¢J dew-point, and the honeycle version delivers down to -50¢J or
even lower. Dry air capacities of the twin-tower version are 60 and
110 m³/hr, and the honeycle version
are from 100 up to 1500 m³/hr. The honeycle
version can be used for connecting with several hot air dryers which
are to be either machine mounted, or to mount with the dehumidifier to form
an integral system. All units are adapted with solid-state control and built
to comply with CE safety requirements. Built-in process heater and dew-point
monitor can be fitted to all models as optional features. |
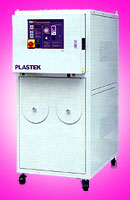 |
 |
|
Hopper
Loaders
Here are two versions available, "integral" and "separate",
both are
suitable for individual conveying of free-flowing virgin granules and regrind
from the floor-mounted material tank to the machine. The integral version
uses either single-phase or three-phase suction motor which is mounted above
the hopper lid, maximum conveying capacity can be up to 300 kg/hr, optional
self-filter-cleaning and cloth filter as well as eye-glass with electrical
level sensor are available. The separate version places the three-phase
suction motor and controls in a separate floor mounted unit and leaves only
a hopper bowl on the machine, maximum conveying capacity can be up to 700
kg/hr, cloth filter and reverse action filter cleaning also eye-glass with
electric level sensor are optionally available on some models. All units
are adapted with microprocessor control and built to comply with CE safety
requirements. |
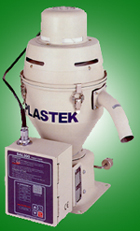 |
 |
|
Mould
Heaters
Here are two versions available, "water" and "oil", both are
suitable for accurate temperature control of the mould. The water version
uses water as heating medium and processes under direct cooling method for
heating up to 95¢J (The indirect-cooled "high-temperature" type up to 140¢J),
maximum pump output can be 100 litre/min in terms of 3 bar discharge pressure.
The oil version uses heat transfer oil (The "high-temperature" type
uses high temp oil) as heating medium and processes under indirect cooling
method for heating up to 160¢J (The "high temperature" type up to 200¢J),
maximum pump output can be 60 litre/min in terms of 3.5 bar discharge pressure,
and leak prevention function is fitted as standard feature. All units are
adapted with solid state control and built to comply with CE safety requirements.
|
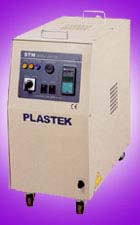 |
|
|
Water
Chillers
Here are two versions available, "air-cooled" and "water-cooled",
both are suitable for cooling the plastics machines and moulds down to 5¢J.
P.I.D. temperature controller with digital setting and display of chilled
water, Grundfos water pump, Copeland (or Maneurop) compressor, stainless
steel chilling unit and expansion water tank are fitted as standard. The
air-cooled version has been designed for running with no requirement
for a cooling tower, and offers cooling capacity from 5,600 to 83,000 Kcal/hr.
The water-cooled version suitable for operating in an ambient temperature
of 35¢J and above, and offers cooling capacity from 8,800 to 180,000 Kcal/hr.
All units are adapted with microprocessor control and built to comply with
CE safety requirements. |
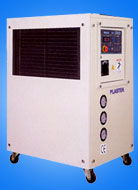 |
 |
|
Granulators
Here are two versions available, "beside-the-press" and "general
purpose". The beside-the-press version possesses a straight up
feeding chute and is therefore particularly suitable for receiving sprue
and runners besides the machine directly from a sprue picker. The general
purpose version is suitable for conveyor-fed or hand-fed of large rejected
moulding parts or components, maximum output capacity up to 900 kg/hr (50
hp motor), full sound-proof on both the feed hopper and cutting chamber,
electrical-mechanical safety interlocks are fitted to all the hinged sections
or removable items, manual collection bin or blower suction bin can be supplied
at the same price. All units are adapted with solid state control and built
to comply with CE safety requirements. |
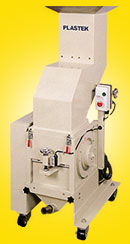 |
 |
|